Background
Healthcare systems in the United States have increasingly turned toward the use of disposable medical equipment in an attempt to save time, lower costs, and reduce the transmission of infections. However, the use of disposable instruments is associated with increased solid waste production and may have negative impacts on the environment, such as increased greenhouse gas emissions.
Objective
The purpose of this study was to inform this discussion; we applied life cycle assessment methods to evaluate the carbon footprints of 3 vaginal specula: a single-use acrylic model and 2 reusable stainless steel models.
Study Design
The functional unit of the study was defined as the completion of 20 gynecologic examinations by either type of speculum. The greenhouse gas emissions (eg, carbon dioxide, methane, nitrous oxide) across all life cycle stages, which includes material production and manufacturing, transportation, use and reprocessing, and end-of-life, were analyzed with the use of SimaPro life cycle assessment software and converted into carbon dioxide equivalents.
Results
The reusable stainless steel grade 304 speculum was found to have a lesser carbon footprint over multiple model scenarios (different reprocessing techniques, autoclave loading/efficiency, and number of uses) than either the reusable stainless steel grade 316 or the disposable acrylic specula. The material production and manufacturing phase contributed most heavily to the total life cycle carbon footprint of the acrylic speculum, whereas the use and reprocessing phase contributed most to the carbon footprints of both stainless steel specula.
Conclusion
The use of disposable vaginal specula is associated with increased greenhouse gas equivalents compared with reusable alternatives with no significant difference in clinical utility. These findings can be used to inform decision-making by healthcare systems, because they weigh a wide range of considerations in making final purchase decisions; similar analytic methods can and should be applied to other components of health systems’ waste streams.
Healthcare in the United States represents a substantial portion of our economy, valued at $2570 billion in 2015 and is associated with 655 megatons of CO 2 equivalents (CO 2e ; 9.8% of the United States total) in 2013. In addition to climbing costs, healthcare facilities are facing the monumental challenge of controlling rising levels of multidrug–resistant infections. To address increased costs and infections, many facilities have increased their use of disposable materials, which typically have decreased upfront costs compared with their reusable alternatives. This shift has further contributed to growing waste production; in 2007, the US healthcare sector produced 4 billion pounds of waste. The factors that contribute to the selection of medical devices include patient safety, clinical efficacy, ease of use, and cost. However, accounting for the environmental impacts of the device across its life cycle (such as increased greenhouse gas emissions, air and water pollution, and solid waste production) should also be included in these decisions, because they represent hidden or externality costs that impact the natural environment and public health.
Why was this study conducted?
The purpose of this study was to determine the CO 2 emissions that are associated with the production, use, and disposal of 3 types of vaginal specula that are used commonly in practice.
Key findings
Reusable stainless steel specula have a lesser carbon footprint compared with their disposable plastic alternatives.
What does this add to what is known?
This study lends support to the supposition that disposable medical equipment items have a more negative impact on the environment than reusable alternatives.
The vaginal speculum is a ubiquitous instrument in healthcare that is used in primary care and obstetrics/gynecology settings for general examinations and surgical and diagnostic procedures. It is unique among medical devices in that, depending on the clinical situation, it can be reprocessed with either high-level disinfectants (such as hydrogen peroxide and glutaraldehyde) or steam sterilization. Disposable and reusable specula differ in production requirements, materials, and need for reprocessing; these differences result in variations in carbon footprint over their lifetime.
Life cycle assessment (LCA) can be used to analyze the environmental and human health impacts of a product across its life cycle with the use of a “cradle to grave” approach. Although still relatively uncommon, the use of LCA is increasing in health-related research, providing valuable information regarding the impacts of healthcare practices beyond the clinic setting. This study applied a LCA framework and approach to evaluate the carbon footprints of reusable stainless steel vaginal specula and single-use acrylic vaginal specula by quantifying the materials, energy, and the associated greenhouse gas emissions at each stage of the speculum life cycle: production, transportation, use, reprocessing, and disposal.
Materials and Methods
We completed a carbon footprint analysis of 3 speculum models that were chosen from a convenience sample of specula currently in use at the Michigan Medicine hospitals and clinics. The specific specula that were studied included the Welch Allyn KleenSpec Disposable Vaginal Specula (Welch Allyn, Skaneateles Falls, NY), the Sklar Merit stainless steel grade 304 Graves and Pederson vaginal specula (Sklar Surgical Instruments, West Chester, PA), and a surgical grade (stainless steel grade 316) specula comparable with the Sklar model. The grade 316 stainless steel contains a higher percentage of molybdenum, which makes it more resistant to corrosion and thus likely to last for a longer period of time than grade 304 steel, although there are no current recommendations regarding the appropriate service life. No coatings or other grades of stainless steel were considered. The scope of our analysis ( Figure 1 ) includes extraction of material and energy resources, manufacturing, transport between various sites in the production process and to the hospital, reprocessing, and disposal at end of life. Possible reprocessing options included autoclaving for sterilization or high-level disinfection with hydrogen peroxide. There were no life cycle data available on other high-level disinfectants, such as glutaraldehyde or ortho-phthalaldehyde, so these were excluded from the scope of this study.

In the life cycle assessment, the basis of comparison is called the “functional unit.” For this study, the functional unit of both disposable and reusable specula was defined as the completion of 20 gynecologic examinations by each type of instrument. The LCA software package (SimaPro 8.5.2; PRé Sustainability, Amersfoort, The Netherlands) was used to conduct the majority of the analysis. The databases used include Ecoinvent 2.2, IDEMAT, GREET, and WARM. Total carbon footprint was assessed as kilograms of CO 2e released, which is a common measure of global warming potential impact.
Modeling
Production phase
Manufacturer data were obtained regarding speculum and packaging composition and weight ( Table 1 ). If the material was unknown, assumptions were made based on relevant literature ; more detailed information from suppliers would allow for a more accurate analysis. Materials that were excluded from the analysis were inks, bulk packaging, autoclave production, illumination pack for plastic specula, and lubrication; these were expected to have minimal impacts on the final results. No specific data were available from manufacturers regarding production of the specula; injection molding was assumed for the acrylic specula and a combination of hot extrusion, milling/turning, deformation, and heat treatment was assumed for the stainless steel specula, based on relevant literature.
Material | Product | Weight, g |
---|---|---|
Acrylic | Disposable speculum | 88.28 |
Stainless steel grade 304 | Reusable speculum | 145.2 |
Stainless steel grade 316 | Reusable speculum | 145.2 |
Kraft paper | Sterilization pack | 4.18 |
Polypropylene | Sterilization pack | 3.49 |
Polyvinyl-chloride | Packaging for disposable speculum | 6.13 |
Hydrogen peroxide | High-level disinfectant | 104.4 |
Transportation
Based on manufacturer and general industry data, the acrylic resin that is required to make the disposable specula was assumed to be made in China, from where it was likely to be transported by container ship to Los Angeles, CA, and from there by truck to Skaneateles Falls, NY, where it would be processed to form specula. These specula were then likely shipped from New York to Ann Arbor, MI, by truck, given that 70% of shipments in United States are made by truck, The stainless steel specula were manufactured in Germany with iron that was mined in France, Belgium, and Italy. All transportation within Europe was assumed to be by rail. The finished specula were assumed to be transported via container ship to Philadelphia, PA, then driven by truck to the distribution center in West Chester, PA, and from there to Ann Arbor, MI. Transport of other materials (sterilization packs, high-level disinfectants, or autoclaves) was not included in this analysis.
Use phase/disposal
Reusable and disposable specula were assumed to have equal clinical efficacy. When the disposable specula were entered into use at Michigan Medicine ambulatory clinics, they were removed from original packaging, used for a gynecologic examination or procedure, and then were disposed of, along with packaging, in general waste. Reusable specula were removed from original packaging, sterilization pack, or nonsterile container (depending on clinical need), used for an examination or procedure, and put aside for reprocessing with either high-level disinfectants or sterilization via autoclave; any associated packaging was discarded in general waste.
Before being reprocessed, reusable specula are rinsed or cleaned to remove gross debris. For high-level disinfection, specula were then completely submerged in a 7.25% hydrogen peroxide solution for at least 8 minutes and then rinsed with water before storage. For autoclave sterilization, specula were placed in a heat seal pouch, which is made made of polypropylene and kraft paper, then into the Midmark M11 autoclave (Midmark, Dayton, OH). Manufacturer specifications for pouch setting indicate a maximum power consumption of 1425–1500 W for a 5-minute 270F steam sterilization plus a 30-minute drying cycle. Total kilowatt hours requirements per cycle were assumed to be 0.83125–0.875 kilowatt hours, although this is likely to be an overestimation because the sterilization, likely the most energy intensive step, only lasts 5 of the 35-minute total cycle. The autoclave typically was run with an assortment of pouched instruments, but loading varied significantly. Both grade 304 and grade 316 specula were assumed to be reused over a range of uses (10–500), as tested by sensitivity analysis.
Waste management after disposal was modeled with the use of the EPA WARM model, which estimates the average greenhouse emissions that are associated with the disposal of various materials, such as plastics and metals, in the United States.
Alternate assumptions
Sensitivity analyses were conducted to better elucidate the influence of key model parameters on the carbon footprints of these products. Alternative model parameters include changes in autoclave loading practices and the number of reuses of the surgical grade specula before disposal. Efficiency of autoclave sterilization was also modeled with the use of the GREET database (Argonne National Laboratory, Argonne, IL) on the carbon intensity of different electricity grids throughout the Untied States.
Results
The CO 2 equivalent emissions of the disposable and reusable specula are shown in Table 2 ; the base case that is listed is 20 examinations that were completed by a stainless steel speculum that had been sterilized in a half-loaded autoclave run on the ReliabilityFirst Corporation grid (the grid of Michigan Medicine). Overall, both types of reusable specula had more favorable CO 2 e emission profiles than the disposable acrylic speculum. As demonstrated in Figure 2 , the grade 304 speculum produces fewer life cycle CO 2 e emissions than the equivalent number of acrylic specula after 2 completed examinations (2.11 kg CO 2 e<2.63); the grade 316, after 3 completed examinations (3.11 kg CO 2 e<3.51). Because the grade 304 speculum is less carbon intensive to produce than the grade 316 speculum, its total life cycle CO 2e emissions remain less than that of the grade 316 speculum over a wide range of uses ( Table 2 ), provided that the grade 304 speculum does not need to be replaced earlier than the grade 316 speculum to complete the same number of examinations. If the number of completed examinations extends to 500, the difference between the 3 speculum options becomes more apparent (316–107.52, 304–101.31, acrylic–438.55 kg CO 2 e), with the difference between the grade 316 speculum and the equivalent acrylic specula becoming approximately equivalent to burning 37.97 gallons of gasoline.
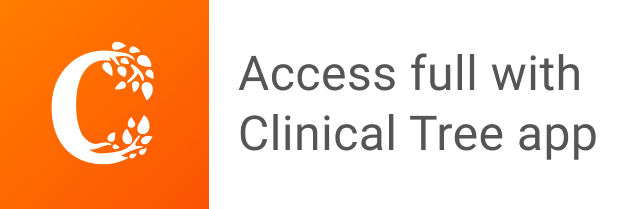